Wood Flooring on Concrete Crying Out for Moisture Protection? Give it This
Installing beautiful wood flooring can transform a home, bringing warmth and style to concrete subfloors. However, without adequate moisture protection, wood floors on concrete are at risk for damage from excess moisture. Left unaddressed, moisture seeping through concrete can wreak havoc on wood flooring in the form of cupping, warping, gapping, and mold growth. The solution is proper moisture barrier installation. Let's explore why wood floors require a moisture barrier over concrete and how to pick the right barrier for your project.
Why Moisture Barriers Are Essential Under Wood Floors on Concrete
Concrete naturally absorbs moisture from the earth and environment. While concrete appears solid, it is actually porous. This means moisture can readily pass from the ground through the slab. Even concrete poured over well-draining gravel is prone to moisture exposure. Groundwater, rain, and other sources will cause moisture to seep upward through the concrete over time.
Additionally, moisture in the air can penetrate through concrete slabs via humidity and condensation. When ambient moisture comes into contact with the concrete's porous surface, it can ingress through the slab. Left unprotected, this moisture migration will cause problems for wood flooring.
The Moisture Problem with Concrete Subfloors
Since wood flooring is installed directly on top of a concrete slab, any moisture coming through the concrete will transfer directly into the wood. Wood absorbs ambient moisture easily. When wood floor planks take on excess moisture, the results are often disastrous.
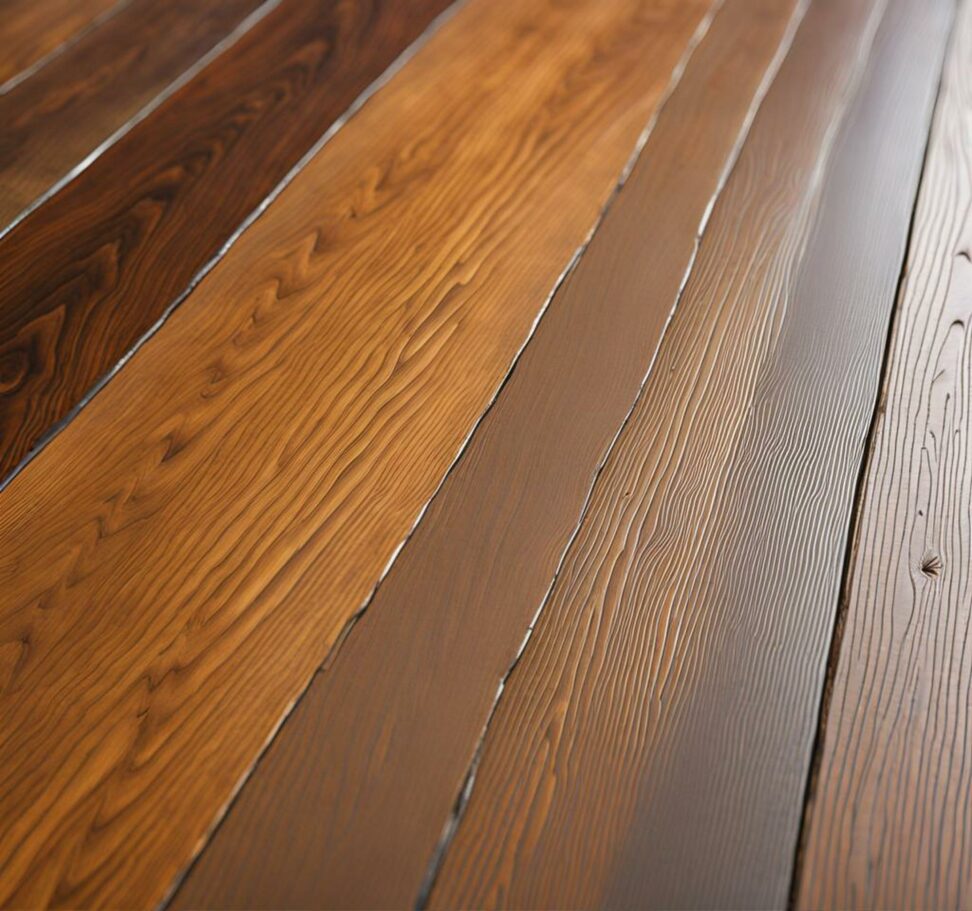
Damage occurs because wood expands as it absorbs moisture. However, concrete does not readily expand and contract. This instability leads to wood floor planks swelling, distorting, and buckling against the rigid surface of the concrete.
How Moisture Damages Wood Flooring
Here are some common ways wood floors are damaged when moisture penetrates from a concrete subfloor:
- Cupping: The wood planks curve up at the edges, forming cups. This results from uneven swelling in the boards.
- Warping: Individual boards bend and twist out of shape from uneven moisture absorption.
- Mold Growth: Trapped moisture promotes mold growth on the subfloor and bottom of the wood flooring.
- Plank Gapping: As planks swell and shrink at different rates, gaps open up between them.
In addition to these visible signs of damage, excess moisture breaks down the internal structure of the wood over time. This can lead to decay and accelerated wear. Catching and resolving moisture problems early is key to extending the lifespan of your wood flooring.
The Purpose of a Moisture Barrier
Installing a proper moisture barrier is the solution for concrete subfloor moisture migration. The barrier blocks groundwater and humidity from permeating into the wood flooring above. It provides a protective layer that separates the porous concrete from the vulnerable wood planks.
Quality moisture barriers are impermeable to block liquid water. However, most allow water vapor to pass through to avoid trapping moisture. This vapor transmission keeps the concrete healthy while safeguarding the wood above.
Keys to an Effective Moisture Barrier
For the best concrete moisture protection, keep these tips in mind:
- Choose an appropriate moisture barrier thickness and material for the project.
- Ensure full, consistent coverage across the entire slab.
- Form a continuous vapor barrier without gaps or punctures.
- Install according to the manufacturer's instructions.
- Seal seams and edges with moisture-safe tape to prevent moisture intrusion.
- Extend barrier 2-3 inches up perimeter walls and columns to prevent moisture migration under the barrier.
With an effective barrier installed, moisture damage to wood flooring can be prevented. Next, let's compare some popular moisture barrier options.
Common Moisture Barrier Materials
There are three main categories of moisture barrier products for use under wood flooring on concrete:
Polyethylene Plastic Sheeting
Polyethylene sheet goods are a popular and affordable choice. Two common options are:
- PE film: A thin polyethylene moisture barrier commonly used over crawl spaces and slabs-on-grade.
- Vapor barrier underlayment: Some underlayments combine a cushioning pad with an integrated polyethylene vapor barrier layer.
Pros: Inexpensive, easy to install, blocks moisture. Can be used in floating floor systems.
Cons: Can be punctured during installation. Seams need to be carefully taped. Not ideal for extremely damp concrete.
Liquid-Applied Membranes
These fluid-applied coatings create seamless moisture protection when rolled or sprayed onto the slab. Products include:
- Epoxy coatings
- Polyurethane membranes
- Moisture-cure urethanes
Pros: Seamless protection, bonds well to concrete. Ideal for slabs with very high moisture.
Cons: More expensive. Can only be used under adhered wood flooring, not floating floors.
Combination Underlayments
These combine foam, felt, or fiber underlayment with a moisture barrier film or coating. Some products are:
- Foam + PE film
- Felt + aluminum foil
- Cork + urethane coating
Pros: Extra cushioning for comfort and sound. Combines two flooring layers in one.
Cons: Multi-layer products can separate over time. Generally more expensive.
With an overview of the main moisture barrier categories, let's look at choosing the ideal product for your project's needs.
Tips for Choosing the Right Moisture Barrier
Consider these key factors when selecting a moisture barrier system:
Consider the Flooring Type
Whether you are installing traditional hardwood, engineered wood, laminate, or bamboo will impact barrier choice. For example, laminate flooring moves more than solid wood and requires dense underlayments to prevent moisture penetration. Meanwhile, denser exotic hardwoods demand maximum moisture protection. Factor your flooring type into barrier selection.
Factor in Installation Method
Glue-down wood floors need a coating that bonds with the adhesive. Floating click-and-lock planks cannot be glued, so a roll-out sheet good is often the best fit. Ensure your moisture barrier works with your installation method.
Test the Concrete's Moisture First
Testing the moisture content of the slab will reveal whether a basic barrier will suffice, or a heavy-duty membrane is needed. Testing also indicates if additional concrete sealing is required before the barrier goes down. Don't install blindly - assess the slab's moisture first.
Selecting the ideal moisture barrier prevents headaches down the road. Next, let's look at proper installation techniques.
Correct Installation Techniques
Meticulous moisture barrier installation is vital. Here are best practices to follow:
- Only install on a clean slab free of dirt, wax, and debris. Etch if needed.
- Plan the barrier layout and seam locations first.
- Run the barrier 2-3 inches up perimeter walls and penetrations.
- Overlap seams 2-4 inches and seal with moisture-safe tape.
- Inspect for rips, gaps, or insufficient overlap and correct before flooring install.
- Avoid walking on the barrier until flooring is installed.
Closely adhering to the manufacturer's instructions is also critical. An improperly installed moisture barrier defeats its purpose entirely.
Signs of Moisture Barrier Failure
If excess moisture penetrates a failed or insufficient moisture barrier, wood flooring damage will occur. Warning signs include:
- Cupped, warped, or gaping floorboards
- Bubbling or peeling finish
- Dark or blackened areas
- Visible moisture on the slab
- A damp, musty smell
- Mold or mildew growth
If you notice any of these issues, moisture has likely breached the barrier. Next, we'll explore troubleshooting solutions.
Troubleshooting Excess Moisture Issues
If moisture problems arise, take these corrective steps:
Further Moisture Testing
Use moisture meters at problem areas to identify if moisture is exceeding recommended levels for the wood flooring. Testing pinpoints barrier weak points.
Barrier Repairs or Replacement
Inspect for punctures, gaps, and seam failures. Make repairs following manufacturer guidelines. For widespread failure, full replacement may be necessary.
Dehumidification Systems
In areas with chronically high humidity, dehumidifier systems help maintain optimal conditions. They can be installed in basements and crawl spaces.
Catching and fixing underlying moisture barrier issues is key to stopping wood floor damage.
Maintaining Moisture Protection Over Time
Don't assume the moisture barrier is set-it-and-forget-it. Check its condition annually and make repairs as needed. If you undertake renovations or surface prepping that could compromise the barrier, be sure to replace it.
On slabs with continual moisture migration, plan to test and monitor conditions regularly. Ongoing moisture management preserves your wood flooring investment.
Managing moisture is imperative when pairing wood floors with concrete subfloors. Excess moisture leads to cupped, warped, and moldy floorboards. Installing an effective moisture barrier guards against these failures.
From polyethylene sheets to fluid-applied membranes, modern moisture barriers offer complete protection. Match the barrier to your specific flooring and slab conditions for optimal performance. With the right solution in place, you can enjoy beautiful wood floors protected from concrete moisture damage for years to come.