Learn How to Frame out an Affordable Lean-To Roof
Adding a lean-to roof can be a great way to expand your home's livable space while also providing weather protection for a porch, patio or garage. With simple framing and readily available materials, a DIY lean-to can often be built faster and more affordably than other room additions.
We'll cover planning considerations, material selection, tools needed, step-by-step framing instructions, and tips for proper waterproofing. With the right information and a methodical approach, you can successfully build a custom lean-to roof over a weekend!
What is a Lean-To Roof?
A lean-to is a single-sloped roof that is attached to an existing exterior wall of a home or building. The pitched roof rafters only need to be framed on one side, since they sit atop the wall to form the structure. Lean-to roofs are incredibly versatile - they can be built over patios, decks, garages, or against nearly any vertical surface as long as it can structurally support the roof.
Compared to more complex multi-gabled roofs, lean-tos are much simpler to frame out. The open layout also makes them ideal for use as covered porches, carports, storage shelters, and even outdoor kitchens. Lean-to designs are especially popular choices for cost-conscious DIYers looking to add weather protection or expand their living space affordably.
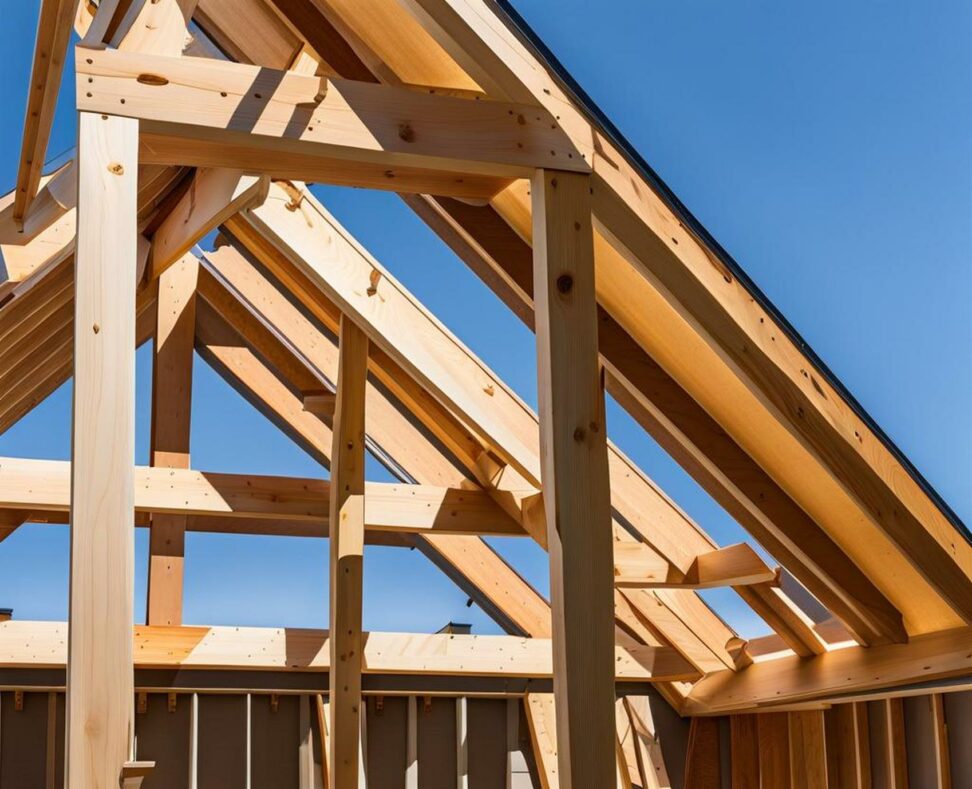
Benefits of Lean-To Roofs
There are many great reasons to consider adding a lean-to roof structure to your home:
- Cost-effective - Single slope simplifies framing and uses fewer materials.
- Versatile - Can cover patios, decks, driveways and more.
- Adds weather protection for outdoor spaces and storage.
- Creates additional "outdoor rooms" for relaxing or cooking.
- Provides shaded area and rain cover for garage or carport.
- Can be used to expand living space by enclosing area.
- Straightforward project for DIYers with basic skills.
Planning Your Lean-To Roof
The first step in any framing project is proper planning and layout. There are several key factors to consider before building your lean-to roof addition:
Location and Size
Determine where you want to build the lean-to and how much square footage you hope to cover. Available space on the existing wall and desired function will guide positioning and dimensions. For maximum cost savings, plan dimensions in 2 ft increments to optimize standard lumber lengths. Often 12-20 ft widths work well.
Height and Pitch
Typical lean-to roof pitches range from 4:12 to 6:12 (18-27 degree slopes). The steeper the pitch, the faster water and snow will drain off. However, a higher pitch also increases the height of the knee wall framing. Finding the right balance for your climate and space is key.
Access and Drainage
Consider how you will access the space under the lean-to roof. Allow for adequate door or window openings as needed. Also plan ahead for proper drainage. Factors like grading, gutters and downspouts will be important for directing water away from the structure.
Permits and Codes
Most lean-to roofs require building permits, especially if attached to existing structures. Building codes provide critical structural requirements. Review local requirements and have plans approved before starting your framing project.
Tools Needed for Framing a Lean-To Roof
You can build the basic framing for a lean-to roof using common woodworking tools. Here are some must-have tools for the job:
- Circular saw - For cutting rafter tails and lumber to length
- Miter saw - Makes precise angle cuts for rafter birdsmouths
- Jigsaw - Useful for cutting openings in existing wall
- Drill/driver - Drives ledger screws and secures rafters
- Level - Confirmsledger board is level before attaching rafters
- Tape measure - Essential for measuring and laying out cuts
- Ladder/scaffolding - Allows safe access to roof framing area
- Clamps - Hold framing pieces securely for faster assembly
Safety gear like glasses, ear protection and dust masks are also a smart investment for any construction project.
Framing Materials
Standard construction lumber is ideal for most lean-to roofs. Here are some typical framing materials used:
Rafters
2x8, 2x10 or 2x12 rafters spaced 16" on center are common. Size is based on span and roof load. Western red cedar offers longevity. Engineered rafters can also be used to allow longer spans.
Ledger Board
2x ledger board anchors rafter tails and transfers load to wall. Should be same width as rafters. Pressure treated lumber is recommended for weather resistance.
Hardware
Galvanized joist hanger nails, hurricane ties, structural screws, and framing anchors are used to securely fasten connections.
Framing the Rafters
With your materials and tools ready, you're ready to start assembling the roof framing. We'll break the process down into key steps:
Install Ledger Board
First, attach a cut-to-length ledger board securely to the existing wall. This gives rafter tails a surface to rest on. Use a level to ensure it is horizontally straight. Secure with 1/2" lag screws every 16" into wall studs or masonry anchors.
Mark Rafter Spacing
Measure and mark centers for each rafter at 16" intervals along the ledger board. These marks will align with the plumb cuts on rafter tails.
Cut Rafter Tails
Cut a pattern rafter with proper angles using rafter framing geometry. Set rafter angle based on roof pitch. Cut plumb tails to sit flat on ledger marks. Use pattern to mark and cut remaining rafter tails.
Secure Rafter Tails
With rafters cut, position tails on ledger marks. Install galvanized hurricane ties on each to resist uplift forces. Toenail rafters to secure or use joist hanger nails.
Complete Rafter Framing
Finish framing by measuring and cutting rafter tops (birdsmouths) to proper length and angle. Install collar ties between rafters for lateral strength.
Types of Rafters
You have options when it comes to selecting rafter material. Here are some of the most common types:
Dimensional Lumber
Standard 2x dimensional lumber from your local home store is cost-effective and readily available. Pine, fir or cedar are common choices for rafters.
Engineered Wood
Laminated veneer lumber and parallel strand lumber allow for longer rafter spans without sagging. Useful for wider lean-tos.
Metal Rafters
Galvanized steel rafters are very strong and don't shrink or warp. Usually require additional purlins for attaching roof sheathing.
Installing Roof Panels
Once the underlying rafter framing is complete, you're ready to add the roof panels. Lean-tos often utilize corrugated metal or multiwall polycarbonate panels which offer durability, weather-resistance, and allow natural light into the space below. Here are some tips:
Multiwall Polycarbonate
Polycarbonate panels are lightweight yet very strong. Measure and cut panels to size. Use rubber mallet to insert aluminum extrusions along the edges. Attach every 12" with screws.
Allow for Expansion
Unlike plywood sheathing, polycarbonate expands and contracts with temperature changes. Leave a 1/8" gap between panel edges.
Use Closure Strips
Close off the ridges between panel sections with aluminum closure strips screwed atop overlapping panels to prevent leaks.
Waterproofing Details
It's critical to properly flash and seal your new lean-to roof additions to prevent moisture issues down the road. Here are some key waterproofing tips:
Install Metal Flashing
Use step flashing pieces along the wall-roof transition. Cover ledger board with drip edge. Flash skylights or vents.
Seal All Seams
Caulk panel seams and closures with exterior polyurethane sealant. Seal roofing fastener penetrations.
Direct Water Away
Use gutters and downspouts to capture roof runoff. Grade soil away from lean-to wall. Keep lower roof areas clear of debris.
Securing Permits
Most jurisdictions require building permits for home additions like lean-to roofs. Permits help ensure your DIY project follows structural codes and is safe. Here are some key steps:
Review Building Codes
Your local building department can provide details on required snow, wind and seismic loads. This guides structural design.
Submit Application
Typically plans, a permit application form, and a small fee are required to apply. An inspector will review.
Schedule Inspections
Most areas require separate framing and final inspections before completing the project. Inspections verify code compliance.
A lean-to roof is an affordable way to expand your living space and provide weather protection. Following the tips outlined here will help you successfully frame out and roof a customized lean-to addition tailored to your needs. Just be sure to do your homework regarding structural requirements, and don't be afraid to hire a professional if certain aspects of the project are beyond your skill level. But for many homeowners, constructing their own simple lean-to roof is a very rewarding and cost-effective way to enhance their home's potential.